Newclip Technics : une référence Tech in Fab !
Quand on lance le co-fondateur de Newclip Technics, Jean-Pierre Podgorski, sur l’histoire de son entreprise, un passionné se révèle ! Visionnaire d’abord parce qu’il met, comme son associé et ses collaborateurs, toute son énergie au service du retour à la mobilité de patients dont les articulations sont abîmées ou les os fracturés. Visionnaire aussi par sa capacité à transformer une pépite en une société HealthTech de renommée internationale, en concevant et fabriquant des solutions de haute technologie en France, commercialisées dans le monde entier. Synthèse de ces échanges inspirants !
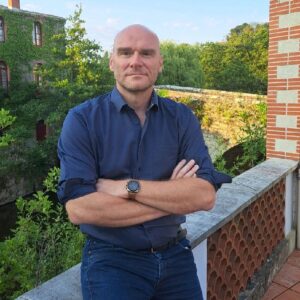
Quand vous fondez Newclip Technics avec Grégoire Larché en 2002, qu’est-ce qui vous anime ?
Nous avions l’ambition de faire progresser le domaine de l’ostéosynthèse par plaque pour les os fracturés (c’est-à-dire le fait de ré-assembler et maintenir des fragments osseux d’une fracture à l’aide de plaques vissées, pour permettre la re-consolidation de l’os, ndlr). Concrètement, nous voulions aider les chirurgiens à réparer ces fractures avec des solutions innovantes, permettant un retour à la mobilité plus rapide des patients .
Jusqu’alors, le monde chirurgical connaissait les plaques métalliques standard, associées à des vis dites non verrouillées (en simple appui compressif sur la plaque), qui obligeaient les patients à rester immobiles jusqu’à consolidation osseuse complète. Puis sont arrivées les plaques dotées d’orifices filetés, à travers lesquelles le chirurgien pouvait insérer des vis dites verrouillées, elles aussi dotées de filetages, qui assurent un assemblage vis-plaque bien plus robuste (monobloc). Ces montages impliquaient néanmoins un positionnement unique (dans un seul axe) de la vis par rapport à la plaque.
Sur ce constat, nous avons pu alors inventer un tout nouveau système de fixation mécanique, associant polyaxialité et verrouillage de la vis à la plaque. Ceci permettait de concilier le meilleur des deux mondes : Liberté d’orientation et performance mécanique. Nous avons breveté la technologie et reçu le soutien de nombreux organismes territoriaux dédiés à l’innovation et au développement économique (Atlanpole, Réseau Entreprendre Atlantique, BPIfrance, le Ministère Français de la Recherche…). Cela nous a permis de nous lancer et d’industrialiser notre solution à grande échelle.
Depuis, nous avons lancé de nombreuses autres innovations (20 brevets internationaux déposés, ndlr) et considérablement élargi nos gammes d’implants et notre offre de services aux chirurgiens. Mais notre leitmotiv, lui, demeure inchangé depuis 20 ans :
Participer au retour à la mobilité des patients, via des solutions d’ostéosynthèse gages d’une consolidation osseuse réussie, respectant le bon alignement anatomique et préservant leurs articulations.
Progressivement vous avez intégré la fabrication de vos produits en interne. Pour quelles raisons ?
Au tout début effectivement, nous assurions la conception mais la fabrication de nos implants était réalisée en sous-traitance. Très rapidement, nous avons décidé d’investir dans des technologies de fabrication de pièces de révolution, avec des machines de décolletage, pour fabriquer notamment nous-mêmes nos vis, nos tournevis… Puis nos plaques ont commencé à présenter une diversité de design et de dimensions (très différentes si elles sont destinées à être posées sur un genou ou un poignet…) qui, pour nous, nécessitait aussi d’internaliser complètement leur fabrication. Nous en sommes donc arrivés à intégrer des machines de fraisage UGV 5 axes.
Nous avons fait ces choix pour préserver notre indépendance et maîtriser notre capacité à nous développer, tout en préservant notre modèle économique et capitalistique. Avec la ferme volonté de maintenir une fabrication française.
Ça ne s’est malgré tout pas fait du jour en lendemain. Il nous a notamment fallu passer par une phase d’apprentissage de l’ensemble du processus, comprendre l’importance de la qualité de la donnée numérique… 18 mois ont ainsi été nécessaires pour intégrer ce savoir-faire et viabiliser notre processus… mais ça valait le coup ! Depuis lors, notre société peut assumer son développement, avec une croissance continue de l’ordre de 15 à 20 % par an. La demande du marché est très forte et nous nous structurons chaque année davantage pour pouvoir y répondre.
En d’autres termes, vous faites partie de la famille « Tech In Fab » ?
Effectivement, nous sommes autant « tech », en développant des solutions se voulant innovantes, que « fab », en intégrant au fil des ans de plus en plus de savoir-faire industriels.
Allier excellence technologique et maîtrise de la fabrication dans le domaine très réglementé de la santé nous permet aussi de structurer des dossiers de validation très solides. Le fait que nous puissions démontrer auprès des autorités compétentes que l’on est maître de l’ensemble des processus clés, de l’idée en passant par la fabrication et la commercialisation, nous aide énormément. Ce modèle et la création de valeur associée nous ont aussi permis de bénéficier de la confiance de nos partenaires bancaires.
L’organisation spatiale de notre société reflète d’ailleurs cette synergie Tech et Fab que nous jugeons vertueuse. Nous sommes localisés à Haute-Goulaine sur 3 sites différents, tous proches les uns des autres pour favoriser le faire-ensemble et partager les mêmes qualités d’exécution, de la conception à la vente en passant par la fabrication.
- Le 1er site abrite Newclip Technics et toutes ses fonctions supports, de la R&D à l’administration des ventes, en passant par le marketing, la qualité, la logistique…
- Le 2ème site se nomme Newclip Manufacturing : il regroupe nos différents moyens d’usinage, là où nous fabriquons nos produits jusqu’au stade dit « semi fini ».
- Et le 3ème site est Newclip Packaging : c’est là que nos implants sont totalement finalisés, à savoir traités en surface, marqués au laser ou encore conditionnés en mode stérile ou non. C’est particulièrement lors de ces dernières phases que nous y intégrons des caractéristiques visant à faciliter leur utilisation au bloc opératoire. Par exemple, nous colorons (par un processus appelé anodisation) nos implants pour éviter toute confusion sur le côté d’implantation (Ex : les plaques dédiées aux membres côté gauche sont bleues). Autre exemple : la fourniture de kits d’ostéosynthèse (plaque, vis et instruments) stériles et à usage unique, permet ainsi aux chirurgiens d’être beaucoup plus réactifs en cas d’intervention en traumatologie.
Chaque bâtiment symbolise ainsi l’indépendance de notre groupe et la maîtrise de nos différents savoir-faire.
Diriez-vous que la vitesse de votre développement s’appuie davantage sur votre capacité à innover ou bien sur votre aptitude à écouter les besoins du marché ?
Ces 2 principes se rejoignent : si nos innovations ne répondaient pas à un besoin, elles n’auraient que peu de succès. Et inversement, si nous ne proposions pas de solutions différenciantes aux praticiens, nous ne bénéficierions pas de leur écoute.
L’innovation ne se trouve pas uniquement dans nos implants, mais aussi dans notre souhait d’accompagner au mieux les chirurgiens dans leur stratégie opératoire. Nous avons par exemple mis en place un service de planification chirurgicale, permettant aux médecins de simuler la réalisation de corrections osseuses (ostéotomies) via la reconstruction 3D de l’anatomie du patient. Pour faire simple, cette planification nous permet de produire ensuite en impression 3D des guides sur mesure, qui vont permettre de réaliser les coupes osseuses, de corriger l’anatomie puis de positionner la plaque et ses vis exactement à l’endroit souhaité par le chirurgien lors de sa simulation. Pour les ostéotomies du genou notamment, de tels outils permettent de simplifier grandement le déroulement de la chirurgie, pour un maximum de précision et de sécurité.
Un autre pan de cette volonté d’accompagnement est notre programme Newclip Faculty : les solutions que nous proposons aux chirurgiens sont technologiques, et leur mise en application peut s’avérer très technique. Nous devons donc permettre à ceux qui nous font confiance d’avoir accès à un apprentissage de qualité. Nous avons ainsi investi dans Skylab, un bâtiment dédié à la formation chirurgicale. Nous y organisons de nombreux cours, la plupart du temps internationaux. L’année dernière, 400 chirurgiens ont été formés par des chirurgiens formateurs de très haut niveau.
L’écoute et l’accompagnement des chirurgiens à l’adoption de nos solutions constituent donc des fondamentaux essentiels à notre action.
Quels sont les nouveaux challenges que vous ambitionnez de relever dans les prochaines années ?
Nous pouvons en cibler trois principaux :
D’abord, nous avons réalisé un chiffre d’affaires consolidé de 49 millions d’euros en 2023. Avec notre plan stratégique, nous ambitionnons de passer le cap des 100 millions d’ici à 5 ans. L’atteinte de cet objectif passera forcément par le développement à l’export. Nous structurons notre modèle de distribution et d’accès au marché avec un mix entre
- une distribution assurée par des représentants dans certains pays
- et notre capacité à monter des filiales commerciales en propre, comme c’est déjà le cas aux USA, en Allemagne, en Espagne, en Belgique, au Portugal, en Australie ou encore au Japon.
Autre défi, durable celui-ci : la ferme volonté de rester en made in France. La crise sanitaire liée au Covid nous a tellement démontré pourquoi il était capital d’être souverain dans le domaine de la santé que nous sommes plus que jamais déterminés à faire perdurer notre modèle hexagonal ! Cela passera notamment par notre capacité à accueillir de nouveaux talents sur l’ensemble des métiers développés au sein de notre groupe, et continuer à investir dans de nouvelles infrastructures sur notre territoire.
Pour finir, nous nous intéressons de près à la distraction articulaire, une stratégie chirurgicale visant à créer les bonnes conditions biomécaniques pour favoriser la production de cartilage articulaire chez de jeunes patients souffrant d’arthrose avancée. Le genou sera notre première cible. Notre crédo est toujours le même :
Proposer des concepts nouveaux permettant de prolonger la durée de vie des articulations plutôt que de les remplacer par des prothèses.
Le talent de vos équipes est un facteur clé de la réussite de votre entreprise. Vos collaborateurs sont-ils comme vous, tous passionnés ?
Nous avons effectivement la chance d’avoir des collaborateurs très impliqués, ils sont nos premiers ambassadeurs et nous en sommes très fiers. Et il est vrai que nous exerçons un métier de passion. Nous essayons de la transmettre dès qu’on le peut pour, peut-être, éveiller des vocations !
Car il nous faut préparer l’avenir de manière proactive en donnant envie aux jeunes générations de nous rejoindre : Notre croissance est en effet corrélée à notre puissance industrielle, qui elle-même dépend des hommes et des femmes qui participeront à l’aventure demain ! Notre équipe RH est donc très mobilisée.
Nous entretenons par exemple des relations privilégiées avec des lycées comme Livet ou la Joliverie, ou encore avec l’UIMM. Nous investissons également beaucoup dans la formation : l’apprentissage et l’alternance pour les futurs talents, mais aussi des programmes de formation interne pour que nos collaborateurs développent leurs compétences. Avis à bon entendeur, nous sommes ouverts à toute forme de partenariat pour faire connaître notre mission et nos métiers au plus grand nombre !